Betterminton
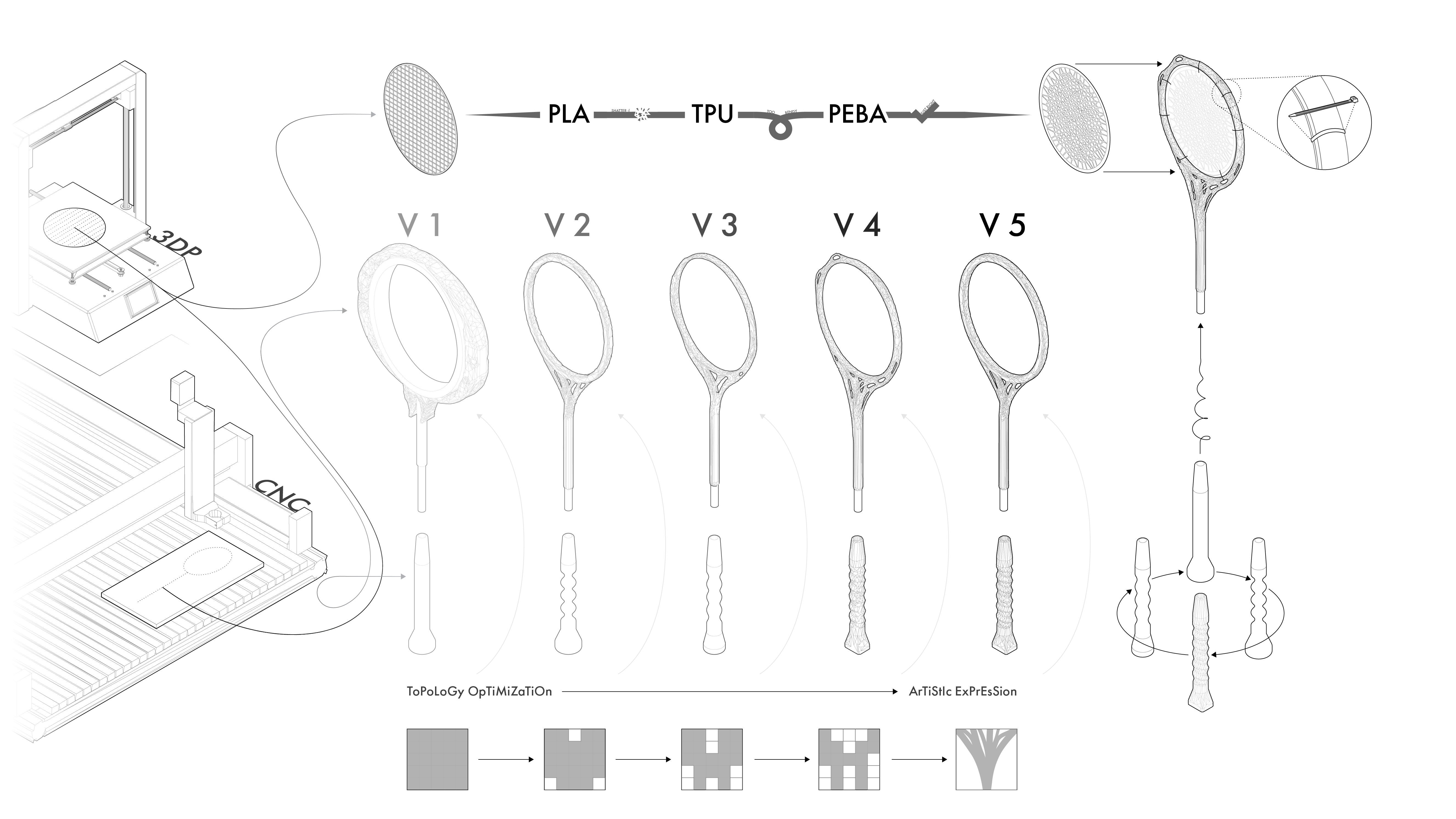
Betterminton, a rapid prototyping exploration in contemporary materials and computational fabrication methods
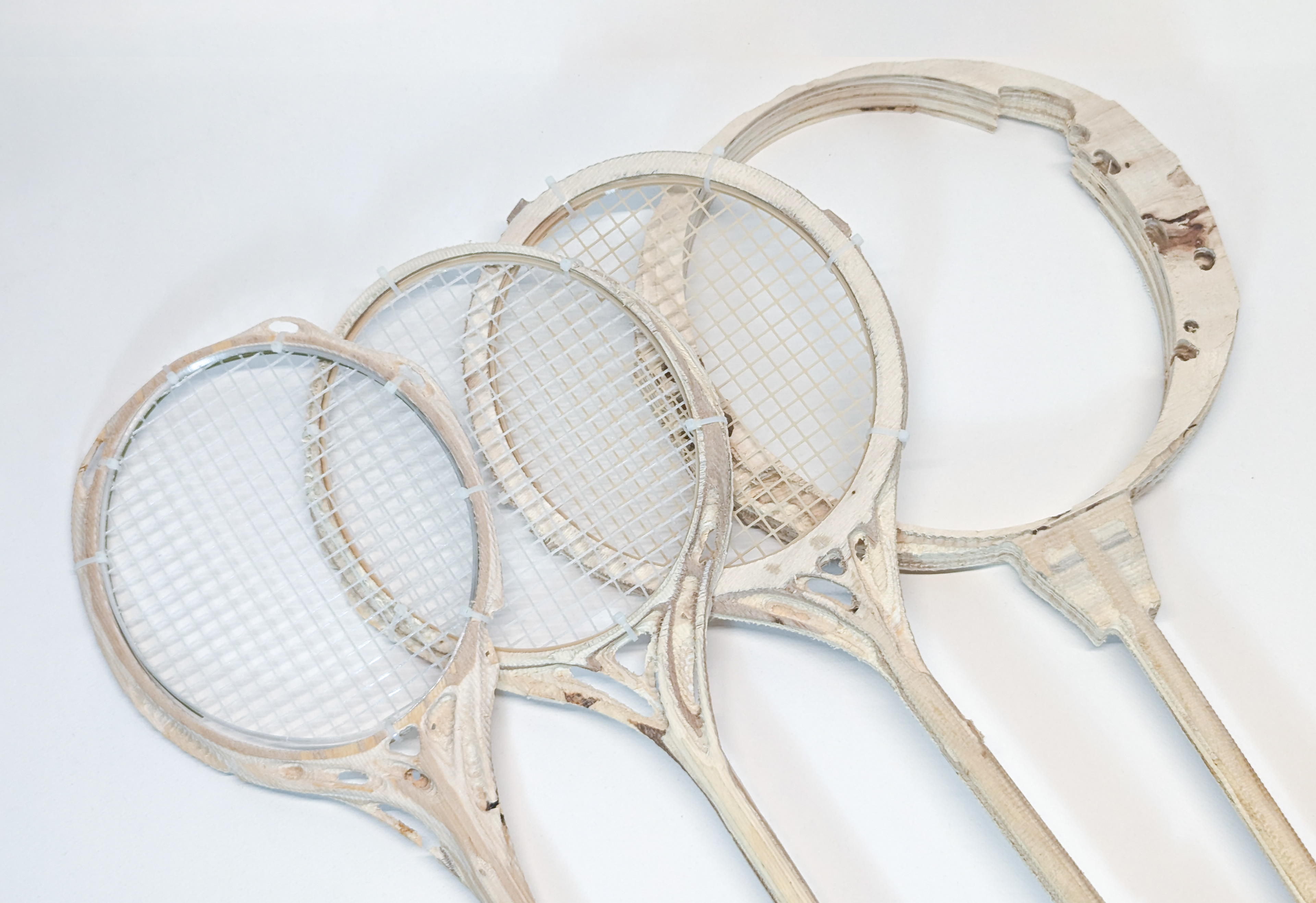

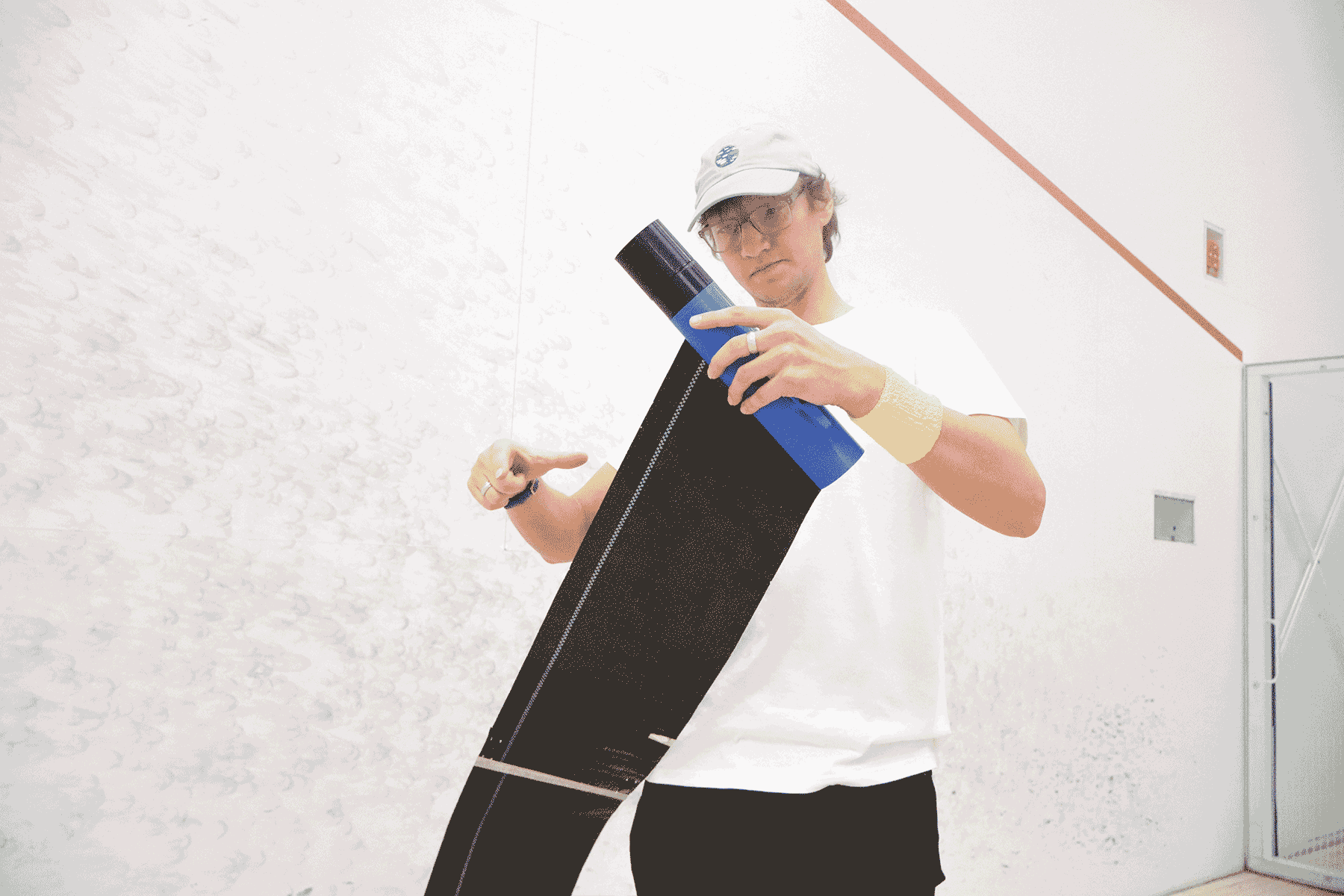
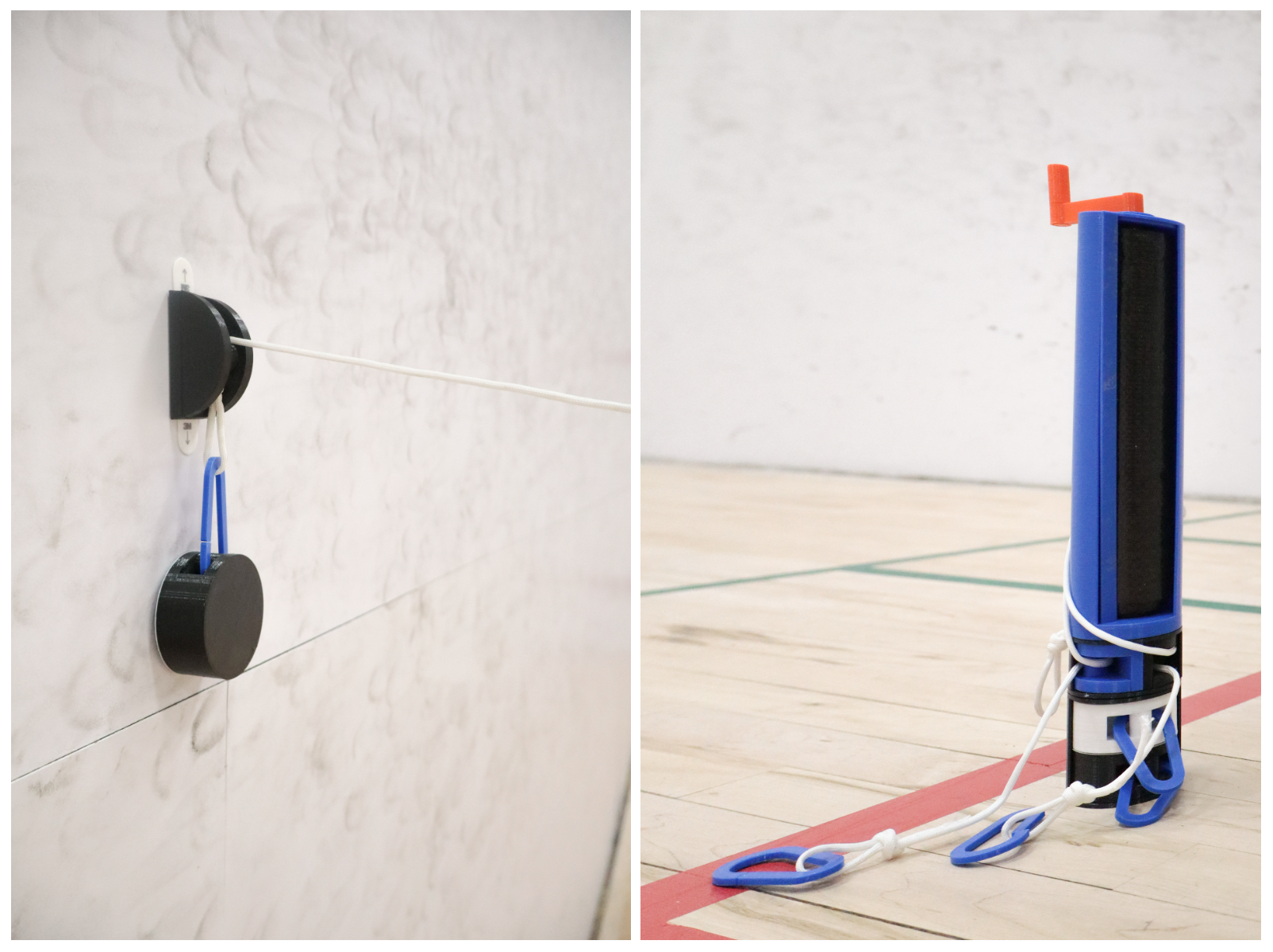
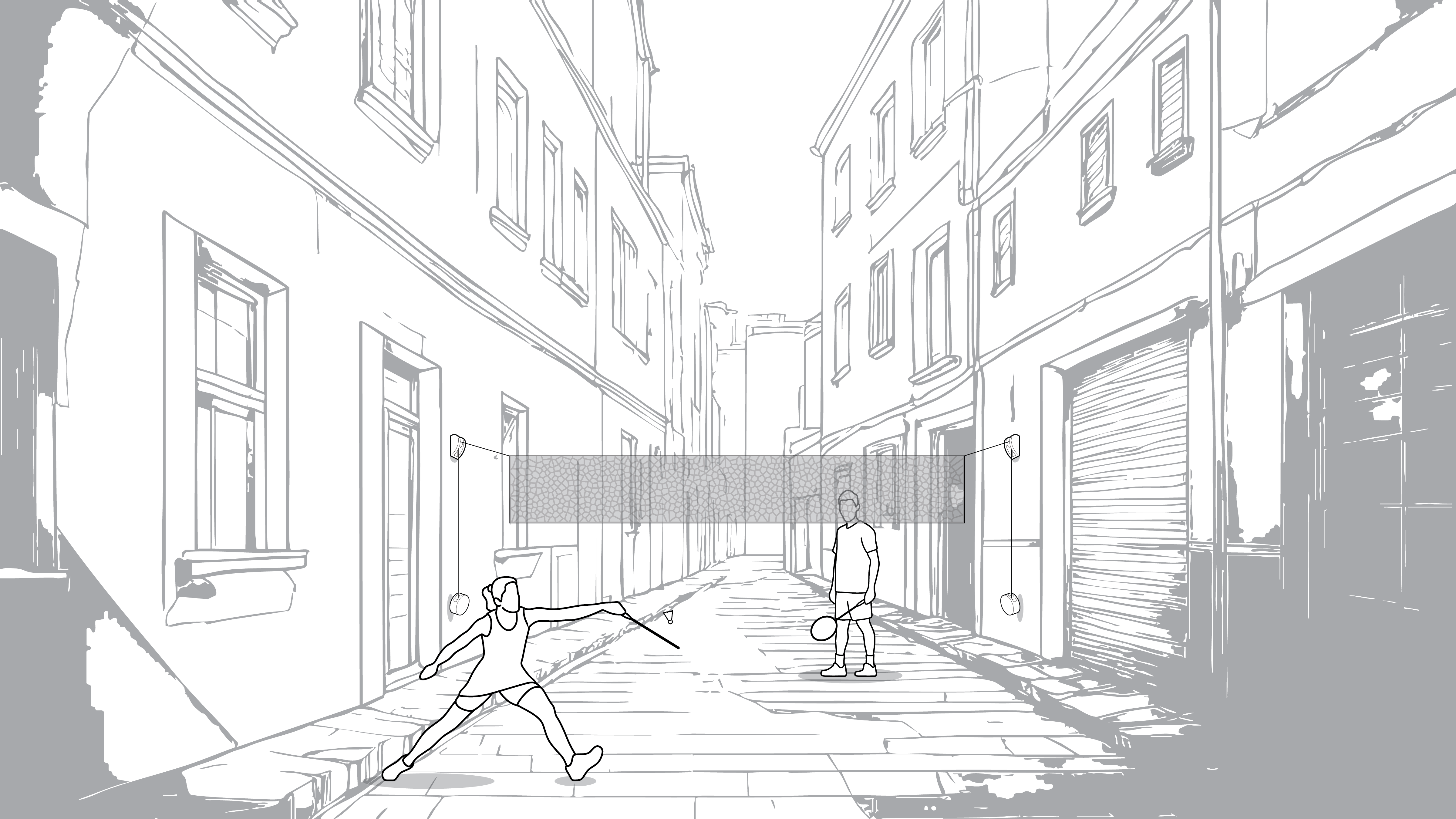
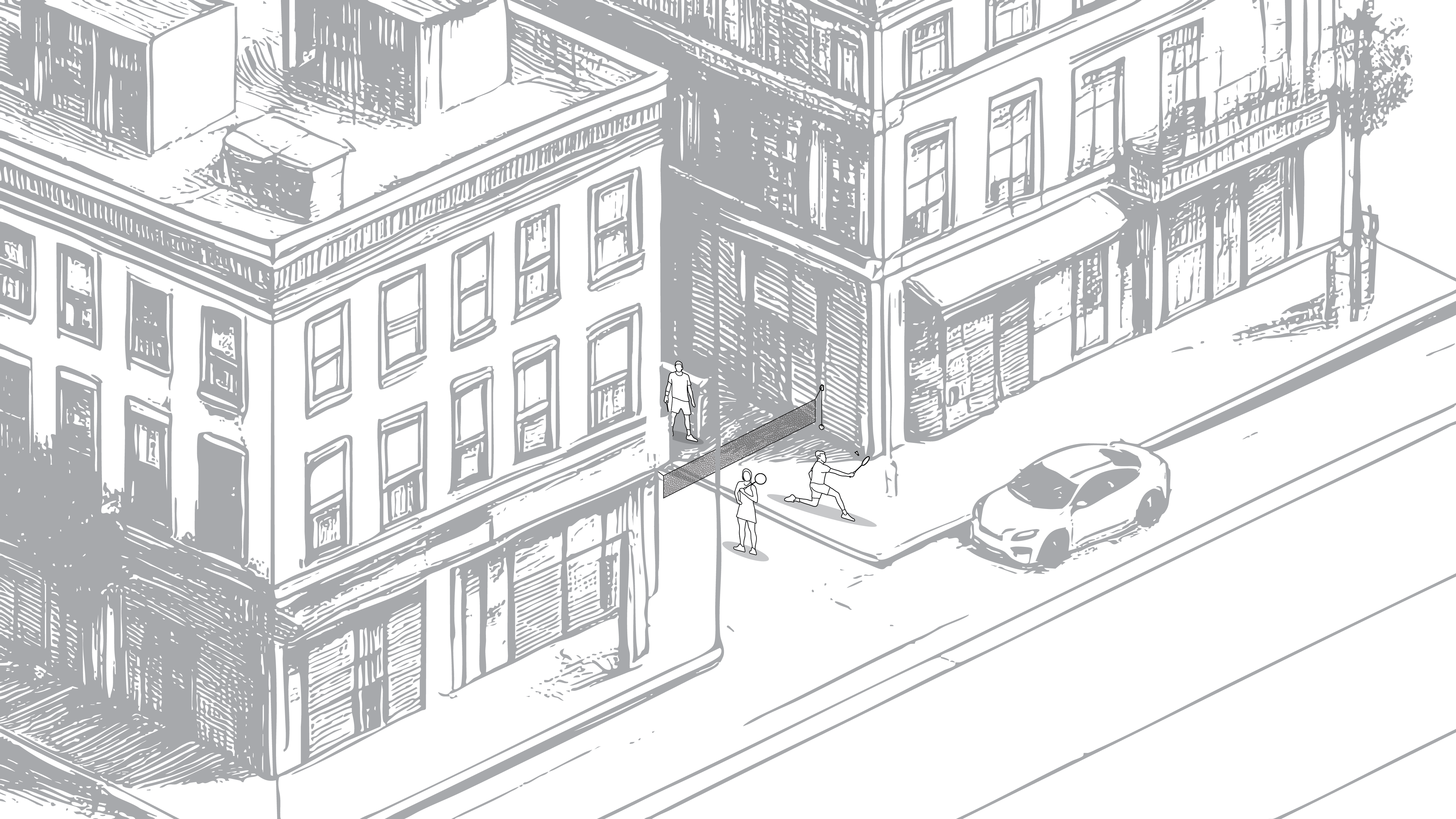
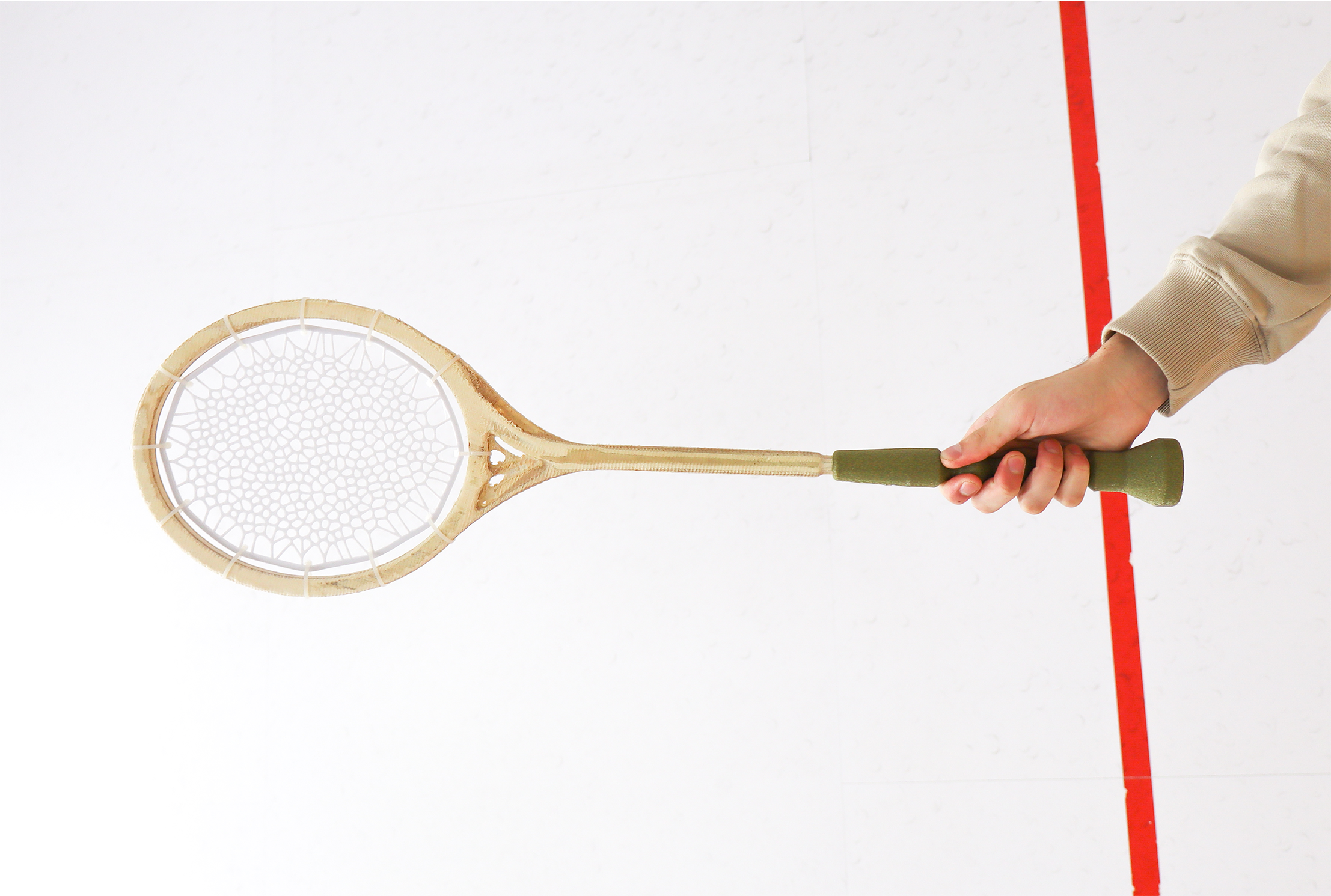
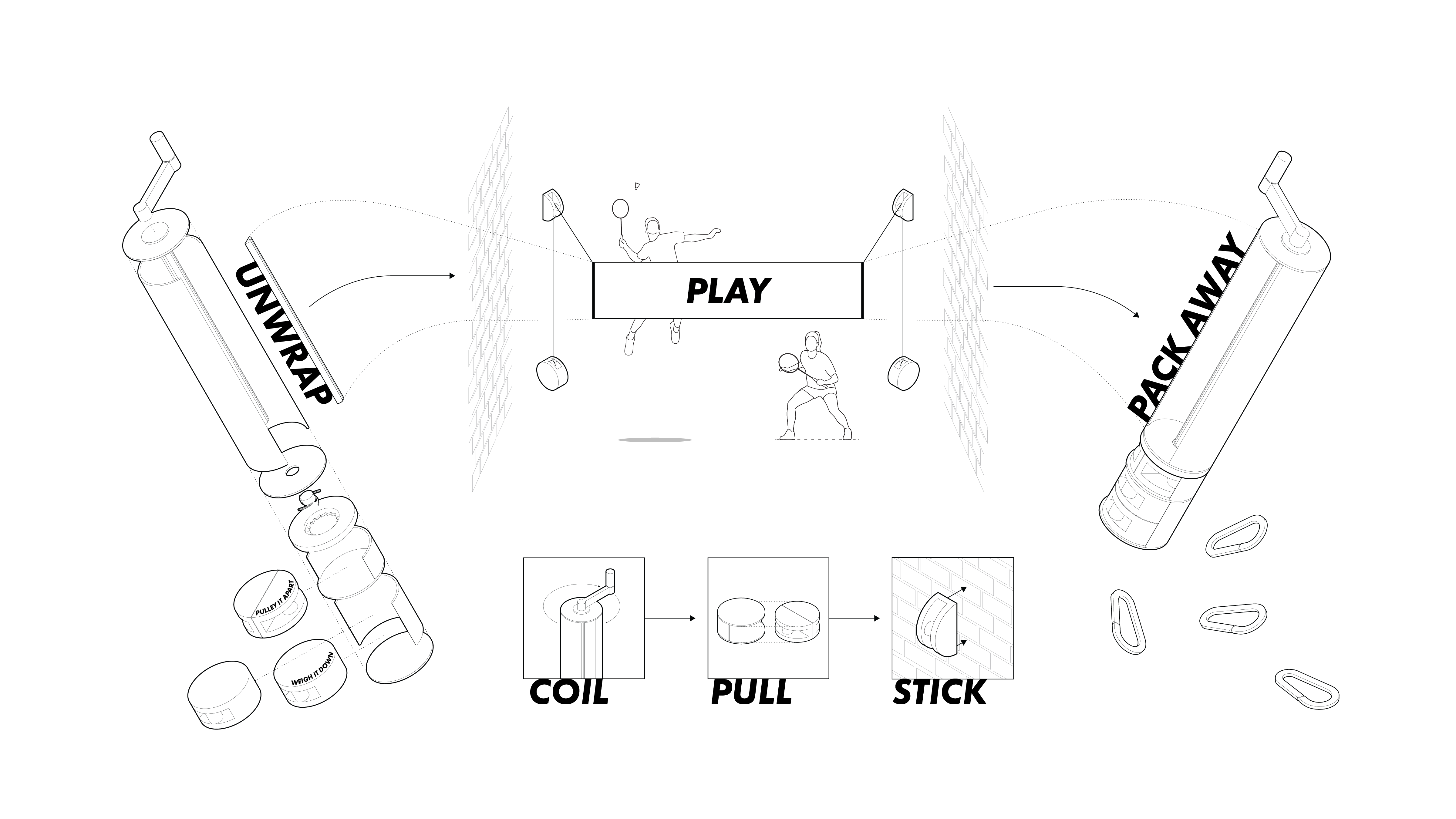
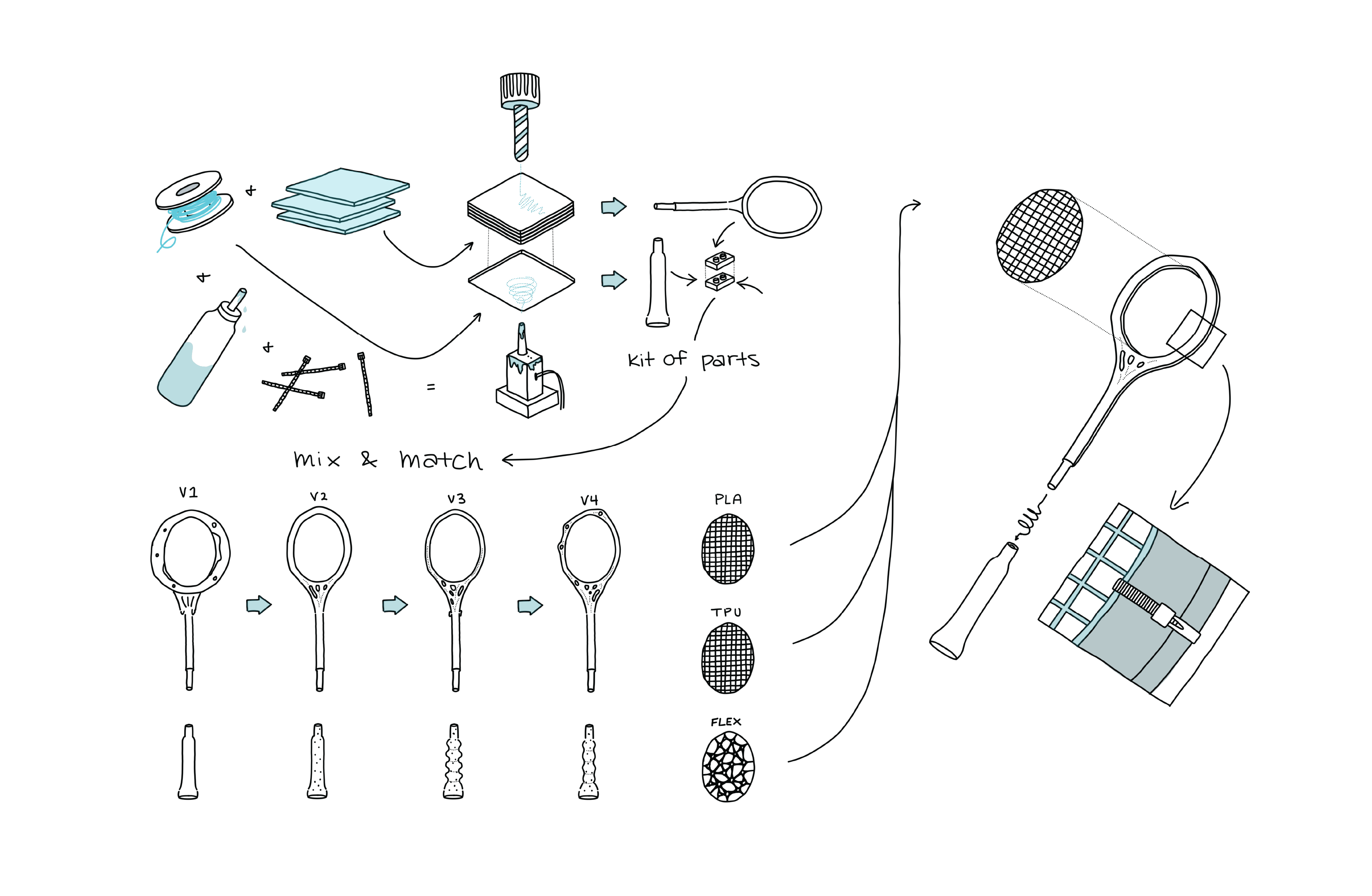
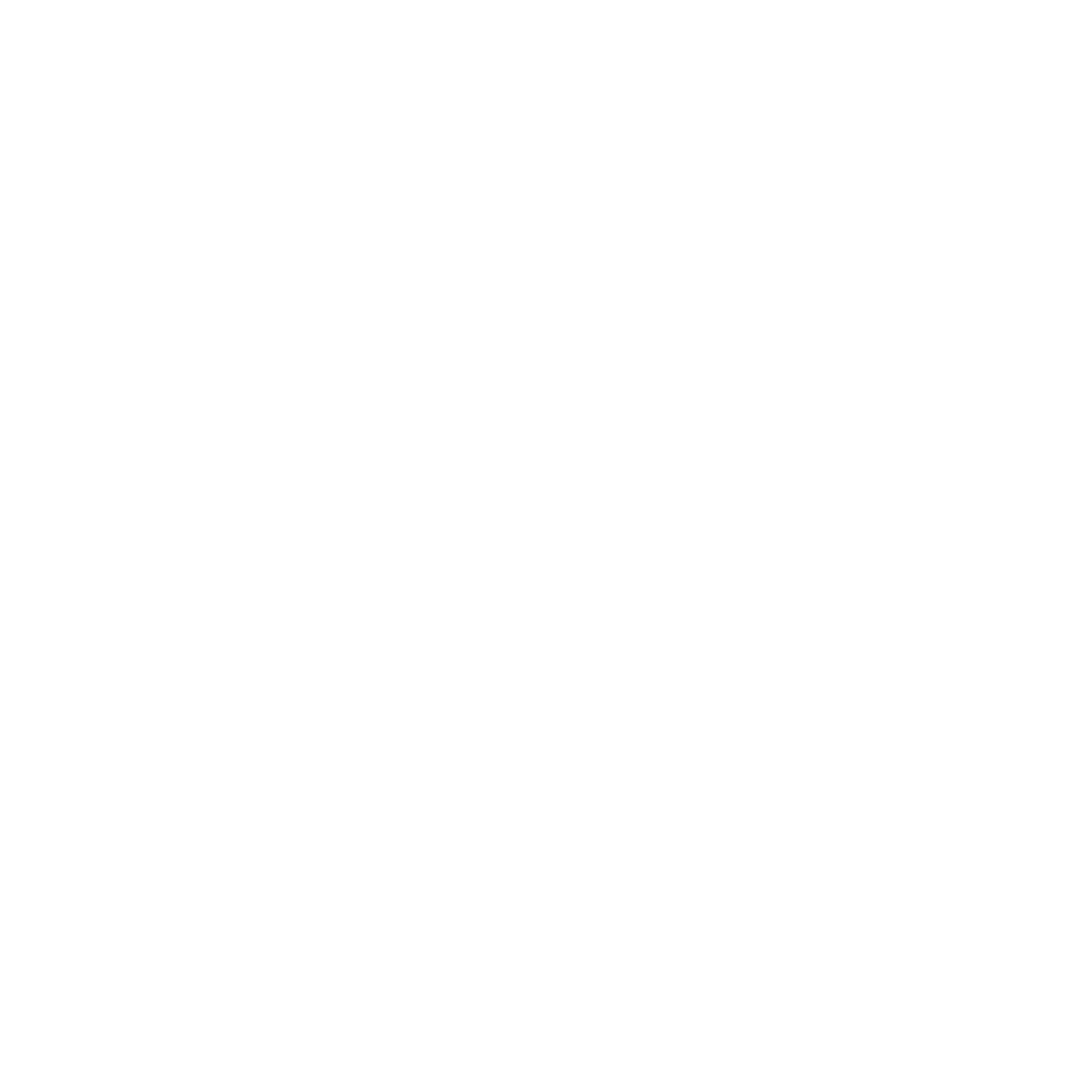
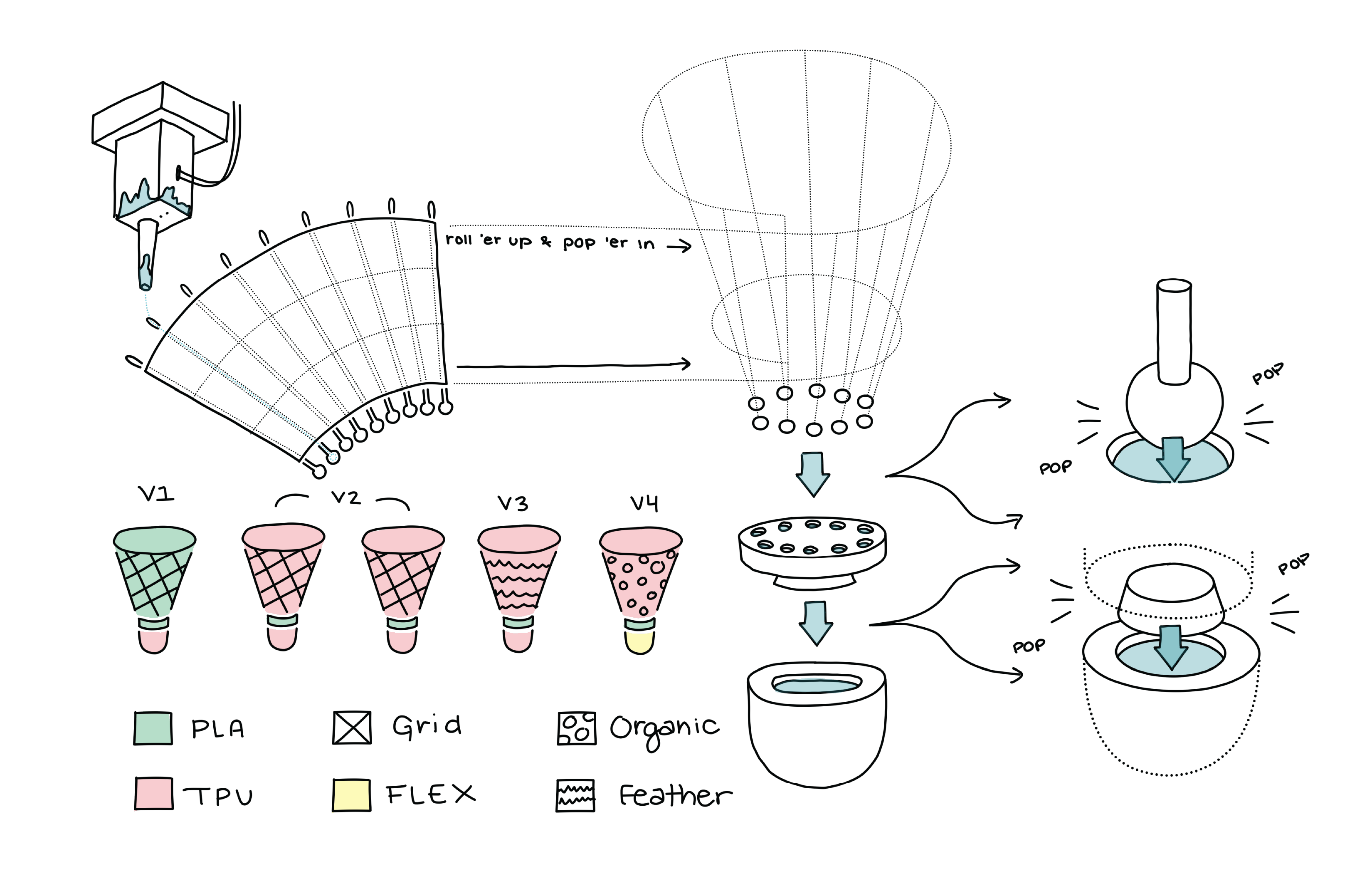
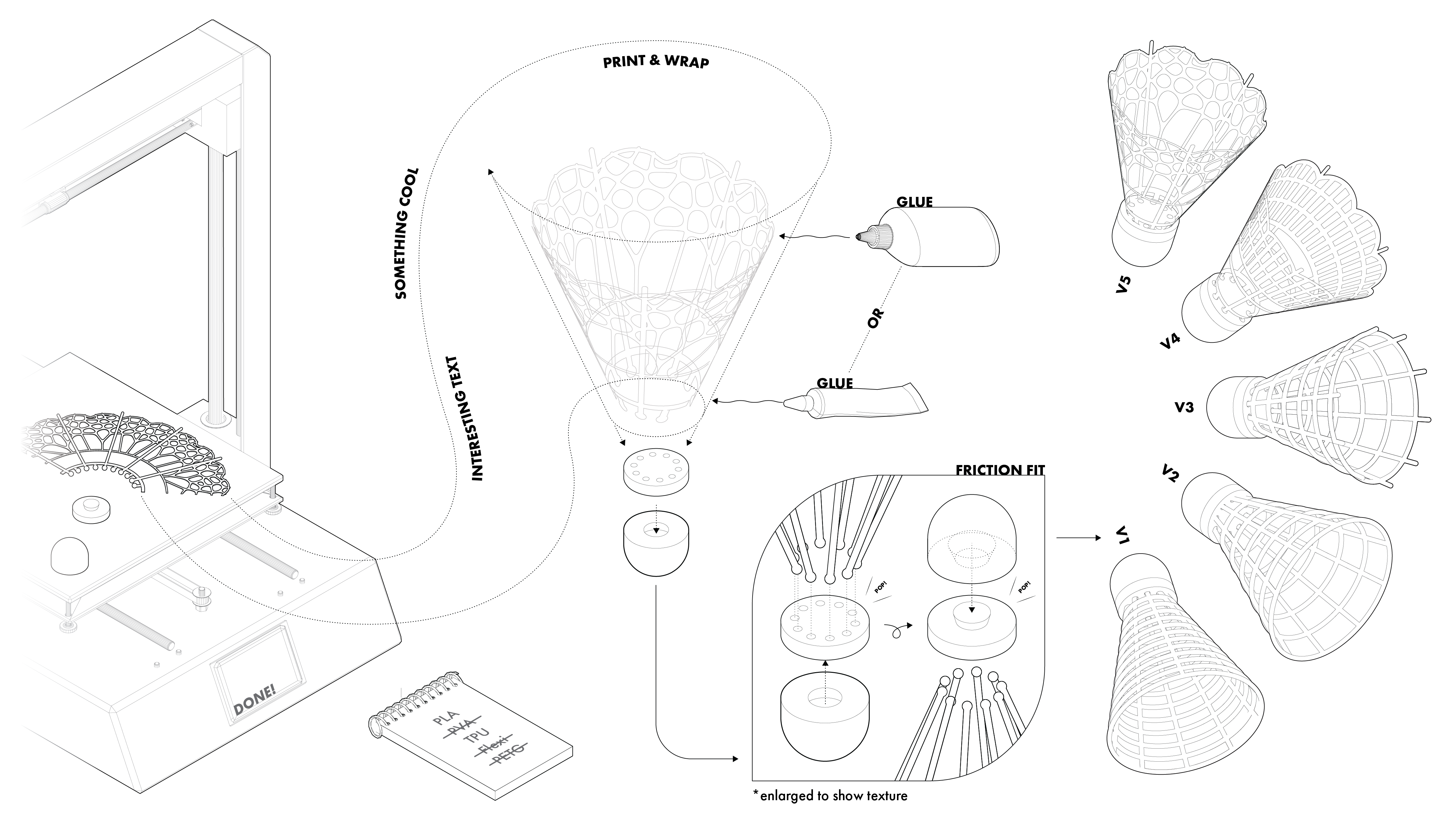
Prompt
Badminton is a historic game with a relatively strict set of expectations and equipment standards - but this can change. Recent advancements in computational design have allowed for new levels of material-efficiency and the revivification of overlooked materials in the contemporary era. Can the use of topology optimization allow for a resurgence of wood-based design in a carbon fiber world? Will my classmates break every one of my prototypes? Only time will tell.
As the sole designer and fabricator for the 'Betterminton' project, I managed every aspect from conceptualization to final presentation. My work involved developing the core premise, conducting research into material capabilities, and performing computational design studies using topology optimization and stress simulations. I handled all concept sketching, 3D modeling, and the creation of detailed diagrams. Furthermore, I undertook the hands-on, small-scale manufacturing of all the wooden and printed prototypes, including multiple iterations of rackets and shuttles, as well as the 'Netcase' intervention, applying techniques like pre-tensioning, compliant hinges and print-in-place mechanisms to achieve the desired performance and aesthetics.
Process
The 'Betterminton' project challenges the rigid standards of traditional sports equipment, asking if computational design can usher in an alternative era of material-efficient, customized, and craft-focused design, even in established domains. Specifically, it explores whether topology optimization can revitalize the use of wood, making it a competitive alternative to modern composites like carbon fiber in applications like badminton rackets. The core motivation is to bridge the often-intimidating gap between advanced computational tools and the hands-on abilities of individual makers, empowering a 'craftsperson-first' approach within a digital landscape.
Tech
• Topology Optimization - BESO for material-efficient structures
• 3D Printer - Bambu Labs X1E, Artillery Sidewinder X1, and Ultimaker S5
• CNC Router - Fully customized and bespoke pathing for CNTMotion 3-Axis flip milling
• 3D Modeling - Iteratively defined compliant models and print-in-place mechanisms
• Material Testing - Conducted elasticity and wear tests on TPU, PLA+, PEBA. and FlexiTough
[Click here to visit the class portfolio site.]